Case Study
Telstar_Hommel
An AR-based support system to dispel costly travel and create a better working environment
Challenges – Keep the production floor running 24/7
Telstar Hommel faced a challenge in quickly resolving problems at its Gyeongju plant. The head office manager in Pyeongtaek often made emergency trips to the Gyeongju plant for technical support. With both facilities within a 4-hour drive, an emergency would mean at least one full day of downtime. This situation also required having experts ready to respond to this emergency at any time, disrupting both professional and personal life.
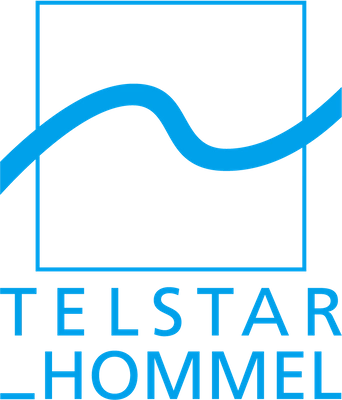
Mirae N Seohae Energy – Leading Gas Supplier
Telstar Hommel is a leading industrial company in South Korea that provides automation and control technology solutions.
They have a head office in Pyeongtaek and a factory in Gyeongju, where they faced a challenge in quickly resolving problems that occurred at the factory.
Introduction
Telstar Hommel operates an automotive parts manufacturing plant in the city of Gyeongju. This plant was dependent on experts and managers located 4 hours away at the Pyeongtaek City headquarters. Telstar_Hommel was looking for an efficient way of transferring knowledge to the manufacturing floor while easing the experts' working conditions.
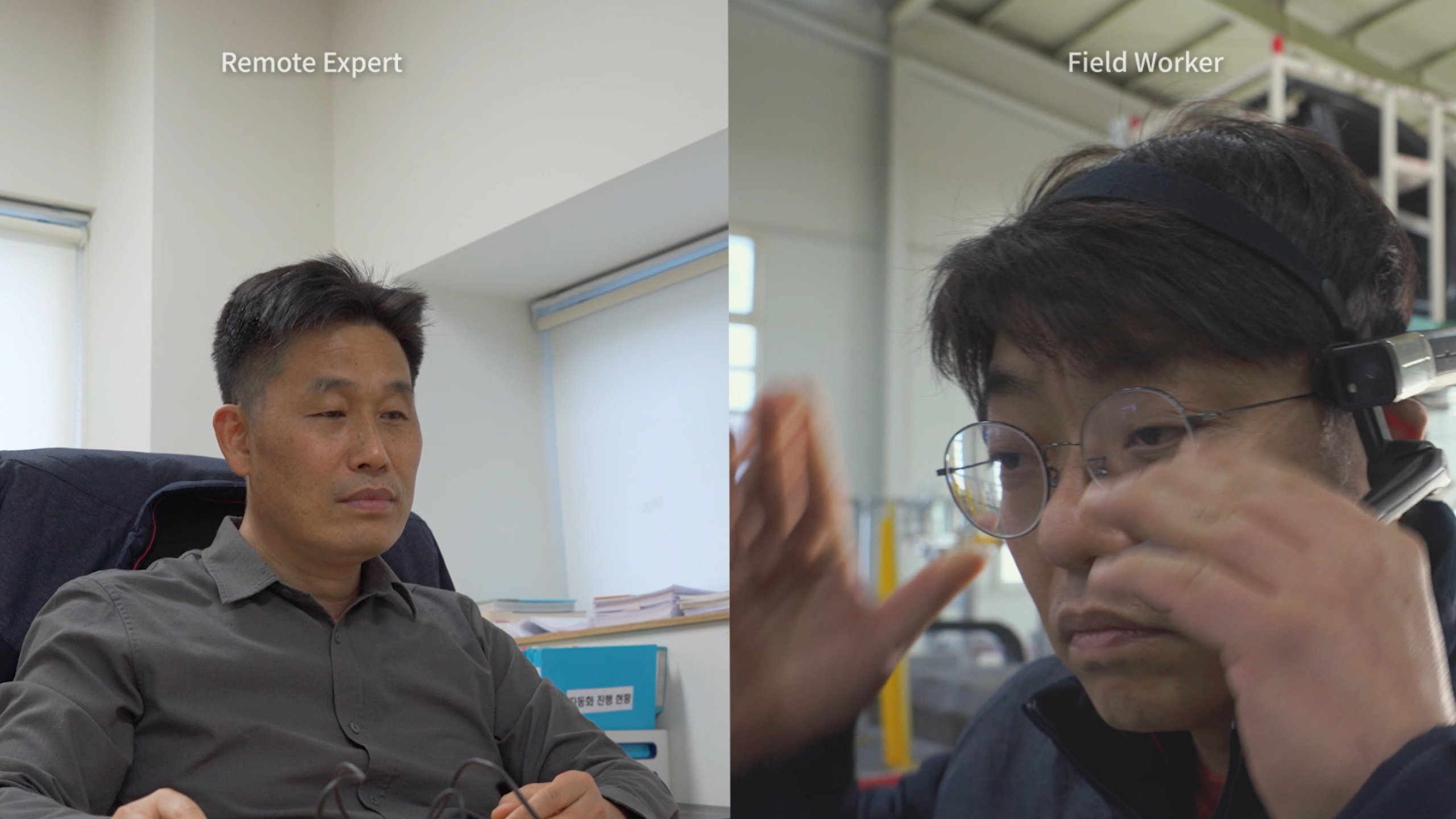
AR-based troubleshooting.
Telstar Hommel implemented VIRNECT Remote to substitute on-site support and eliminate travel time and expenses. Experts at HQ diagnose problems remotely and use AR to guide workers on the field in the corresponding fixing.
VIRNECT Remote allows sharing documents such as schematics and user manuals that workers can refer to on their hands-free wearable devices. They can also get clear instructions using AR pointing and drawing.
Telstar_Hommel recorded the remote collaboration sessions and created reference videos for workers who experienced similar problems. Using VIRNECT Make & View, these guides evolved into in-house-made and maintained AR-based manuals. These manuals help even newly hired workers solve issues, run inspections, and detect risks effectively and independently.
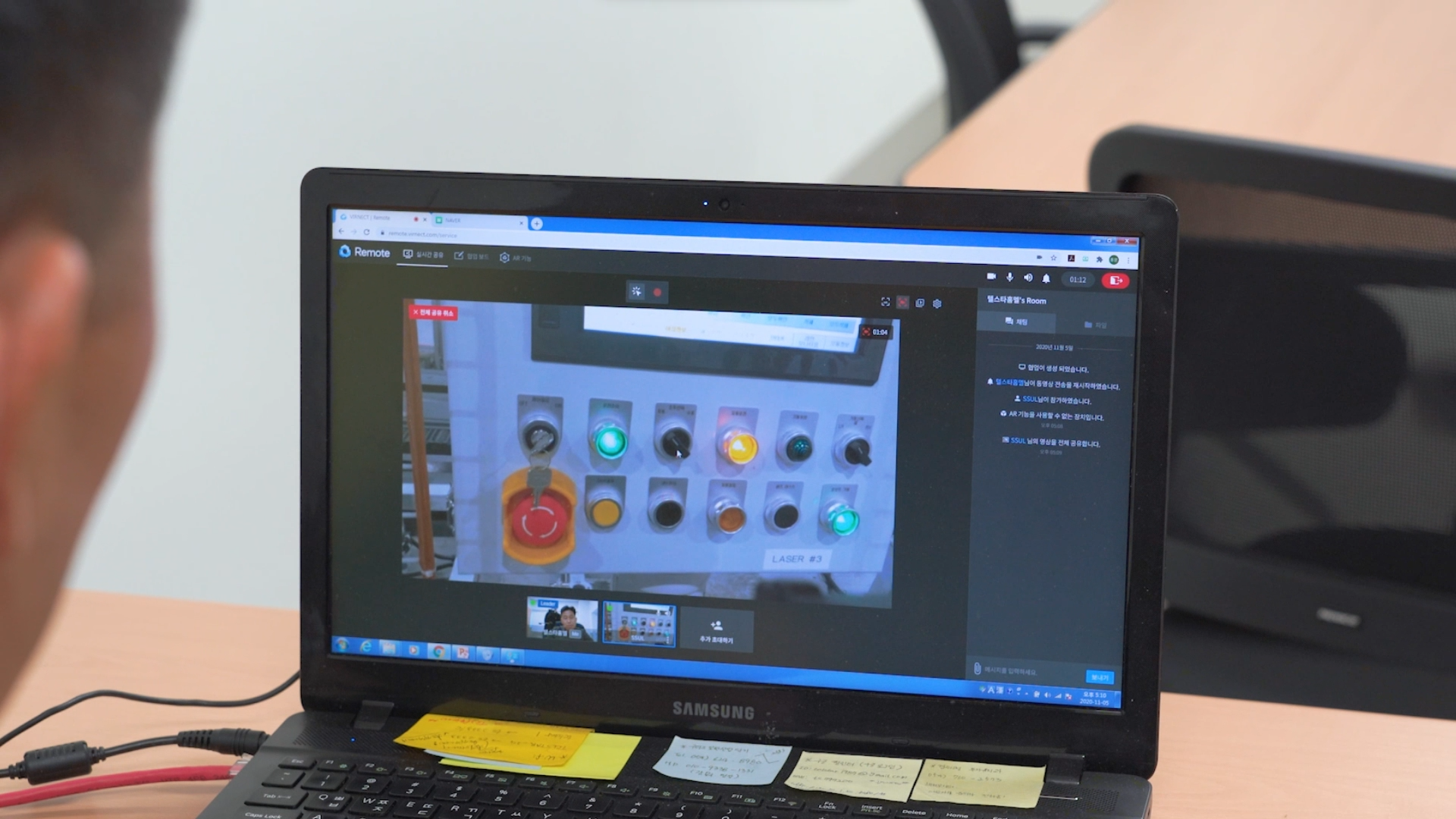
Sharing the expertise during an emergency
The Headquarters runs 24/7 to provide security and safety to customers while monitoring the data. When an alert indicates that some values are out of preset, they send over experts to ensure safety.
VIRNECT’s remote solution connects the experts and the inexperienced maintenance manager. The communication is seamlessly done through augmented reality tools and the sharing of necessary documents. The 3D assets digitized for AR SOPs are also reused to serve communication effectively, yielding further benefits in different applications.
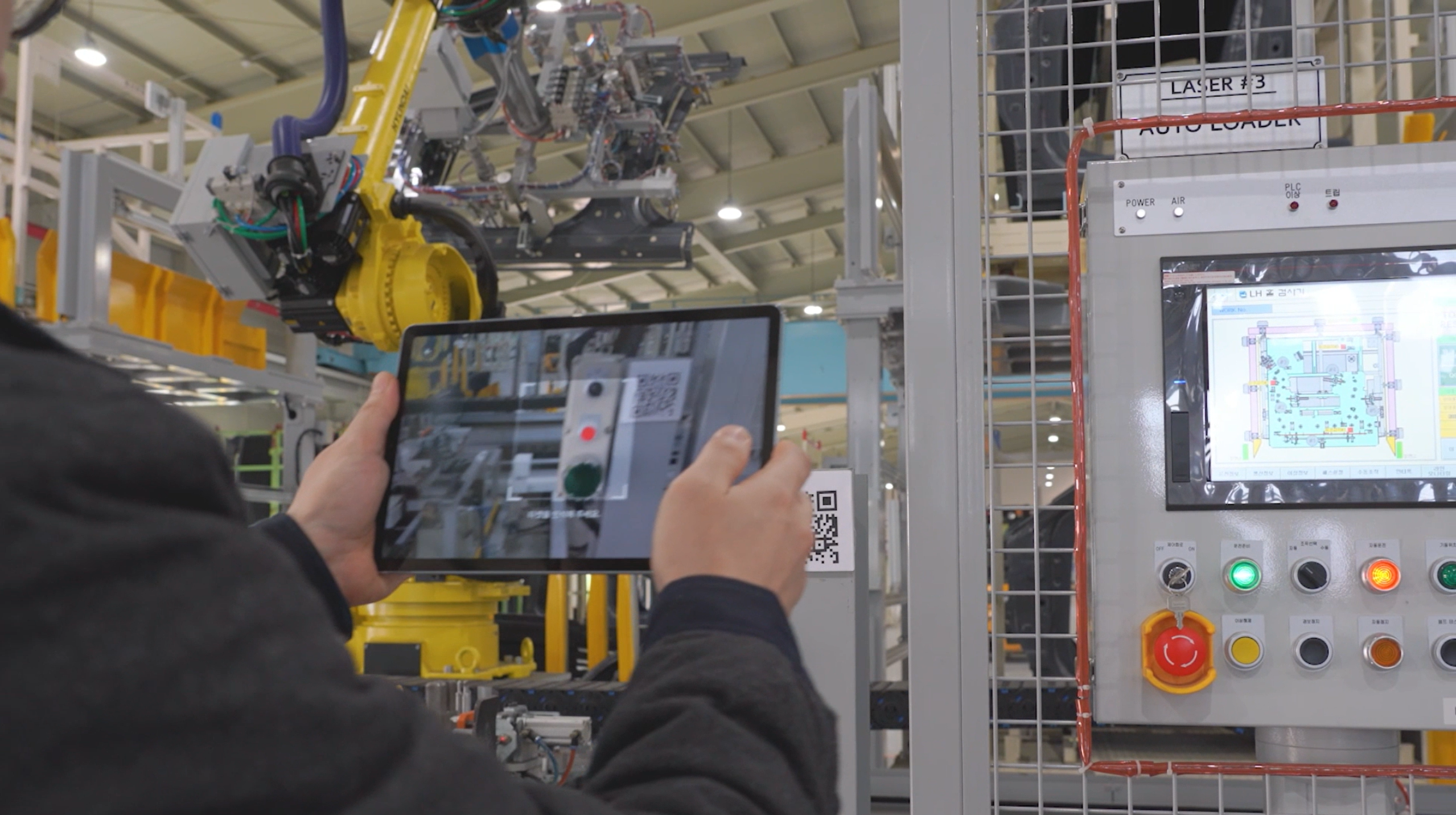
Minimizing downtime and retaining talent
VIRNECT Remote, Make, and View allowed Telstar_Hommel workers to quickly resolve problems and prevent such problems from occurring in the first place.
The emergency response process changed from a minimum of a whole-day to a few minutes. Experts no longer must put everything else on hold and travel from HQ to the production floor whenever there is an emergency. This reduced burden, in turn, reduces the need for travel and increases the experts' quality of life, a key factor for talent retention.
The visual aspect of the system also allowed anyone to see and follow how to operate the equipment, ensuring reduced downtime, travel time, and overall more efficient operations. Additionally, the AR manuals have created knowledge spillovers throughout the production floor workforce.
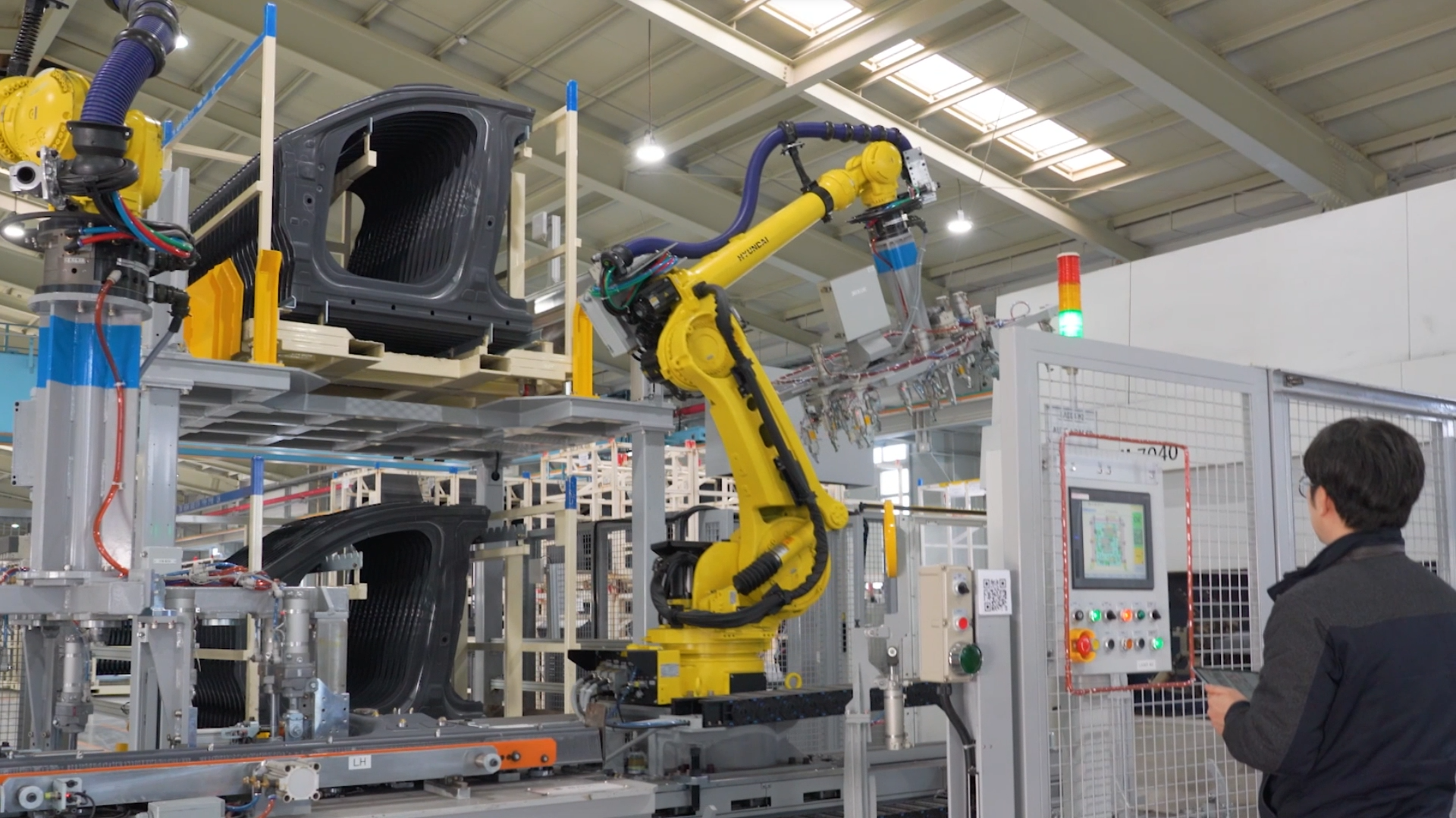
Telstar Hommel's implementation of VIRNECT Remote, Make, and View was a great success in improving the efficiency and productivity of their operations. By allowing workers to resolve problems and troubleshoot themselves, they were able to reduce downtime and travel time and improve overall operations.