Case Study
Mirae N Seohae Energy
An extended reality (XR)-based safety management system for gas supply facilities.
Challenges – Preserving & Democratizing Know-how
Today’s workforce in the Energy sector is aging, making it more challenging to find experienced workers. To prepare for the upcoming challenges of utility companies, Mirae N Seohae Energy was looking for a way to simplify recruiting and onboarding new employees. As the younger generations are digital natives and prefer digital information to codify knowledge, Mirae N Seohae Energy’s executive team has adopted VIRNECT’s XR technology to bring innovation to their workforce. Keeping knowledge within the organization meant a safe and reliable company.
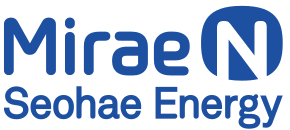
Mirae N Seohae Energy – Leading Gas Supplier
Established in 1995, Mirae N Seohae Energy provides gas to more than 75,000 houses in Korea. Their mission is “To provide more than expected value through energy to the customers” and has provided city gas to various sectors, including commercial, industrial, and residential customers.
Introduction
Seeking to keep a safe working environment, Mirae N Seohae Energy was concerned about the risks inexperienced workers could bring to the operation. As experienced workers become more challenging to secure, they wanted to find a way to improve safety measures and reduce emergency response times while improving onboarding and optimizing inspections.
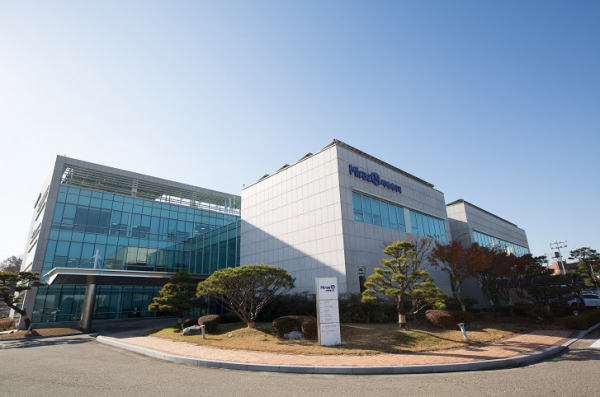
Maintain Knowledge Capital, including Tacit Knowledge.
The maintenance operators are working in more than six different areas in the southeast region, including Dangjin and Seosan. Mirae N Seohae Energy needs to perform regular maintenance on every site with limited resources. They need their new hires to onboard faster and get them up to speed in a reliable yet safe way.
Many facility modules are the same across other facilities in different regions. Among those, many of the recruits in the past had difficulty operating the gas governor, regulator, filter, and Slam-shut valve, making them the perfect candidates for creating efficiencies.
VIRNECT digitized Mirae N Seohae Energy’s physical assets, processes, and know-how to be accessible to many employees in different locations to decentralize knowledge. The biggest hurdle that VIRNECT had to overcome was the broadband speed in some parts of the facility. Reducing the size of each asset to 15MB was needed to bring the digital asset to the screen in 10 seconds or less to maximize the efficiency of learning and performing SOP.
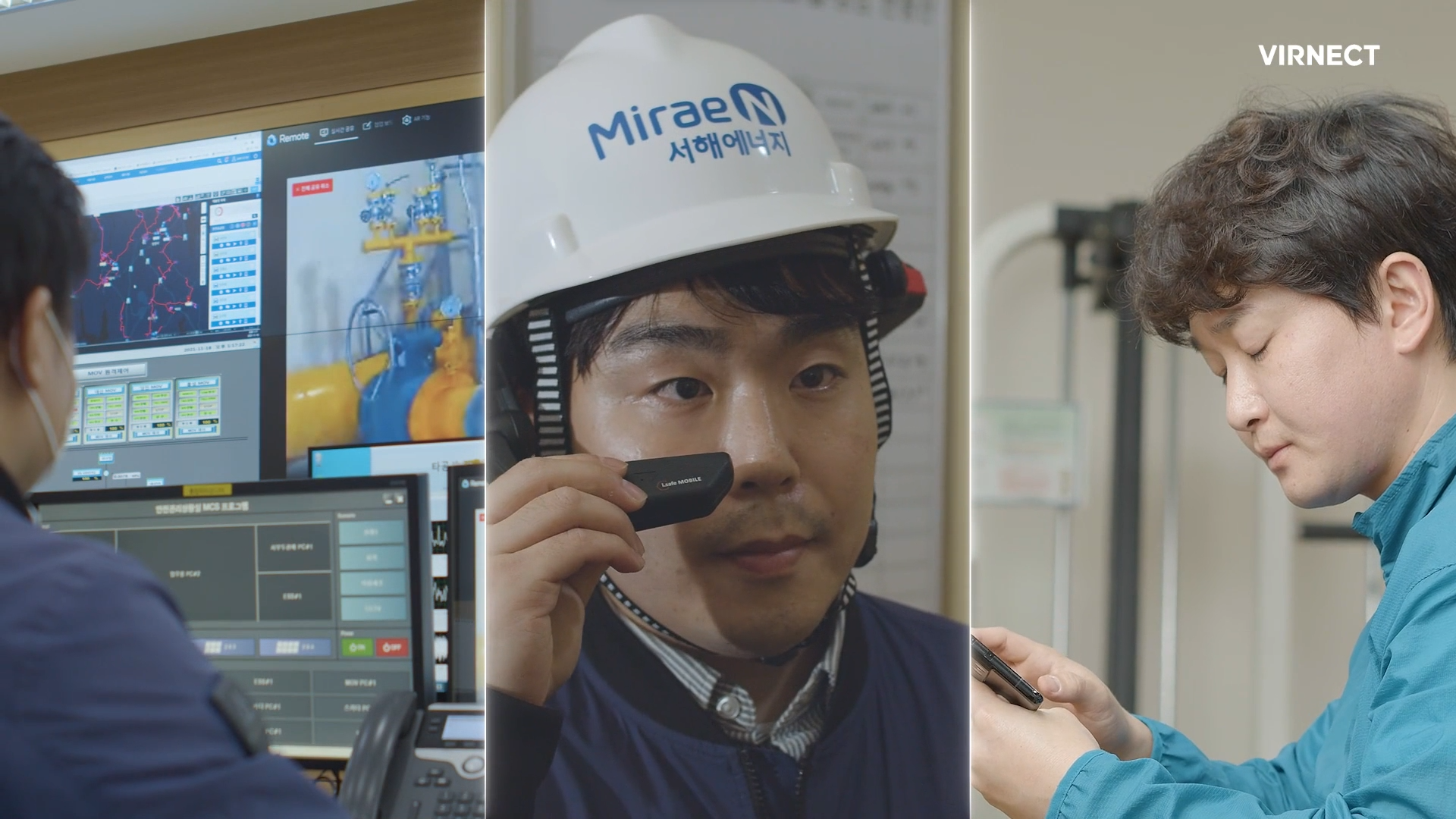
Sharing the expertise during an emergency
The situation room in the HQ of Mirae N Seohae Energy runs 24/7 to provide security and safety to their customers. Mirae N Seohae Energy monitors the data, and when an alert indicates that some values are out of preset value, they send over experts to ensure safety.
VIRNECT’s Remote solution connects the inexperienced maintenance manager with the experts. The communication is seamlessly done through augmented reality tools and the sharing of necessary documents. The 3D assets digitized for AR SOPs are also reused to serve communication effectively, yielding further benefits in different applications.
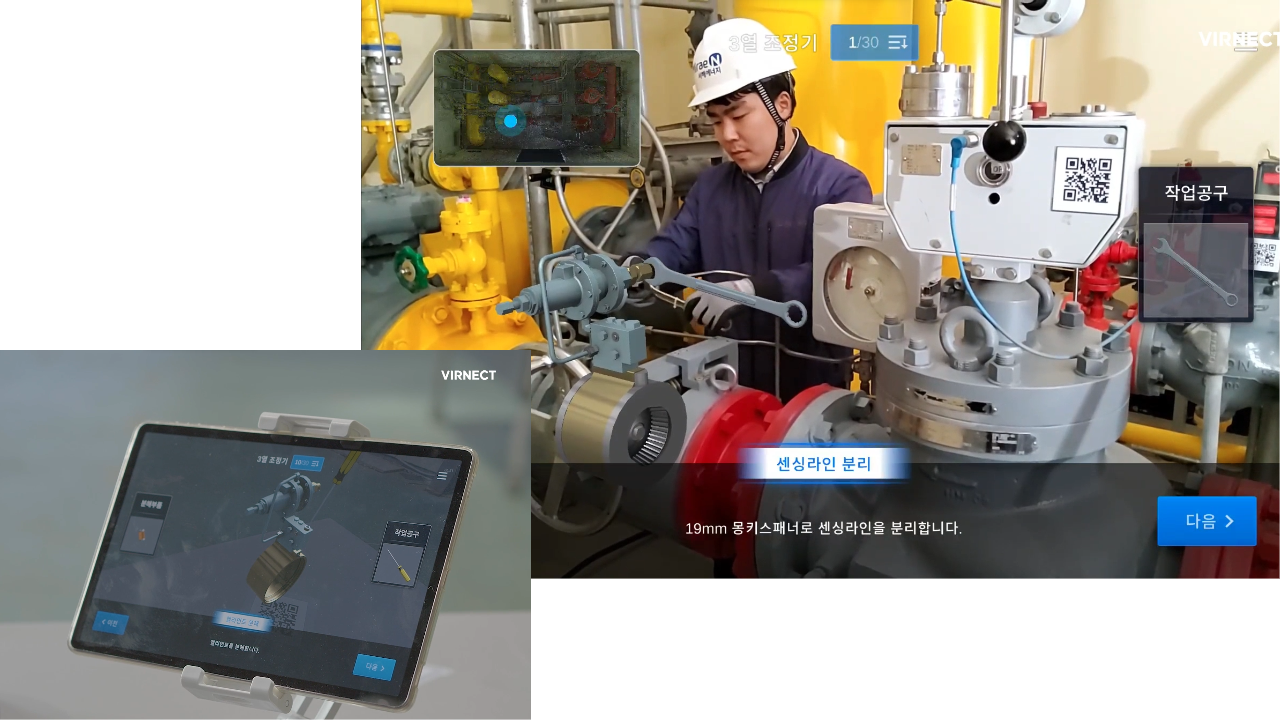
Mirae N Seohae Energy expects reduced time to value and exponential value to recycle digitized assets.
The executive team has empowered its maintenance team with knowledge, making it available to anyone at any moment, with VIRNECT’s knowledge management system.
They have managed to recycle the 3D assets in different applications and consider them used across various departments to maximize their investment. Mirae N Seohae Energy Energy’s journey to XR innovation has begun after the widespread acceptance of change, and VIRNECT will be the technology partner to move the company forward.
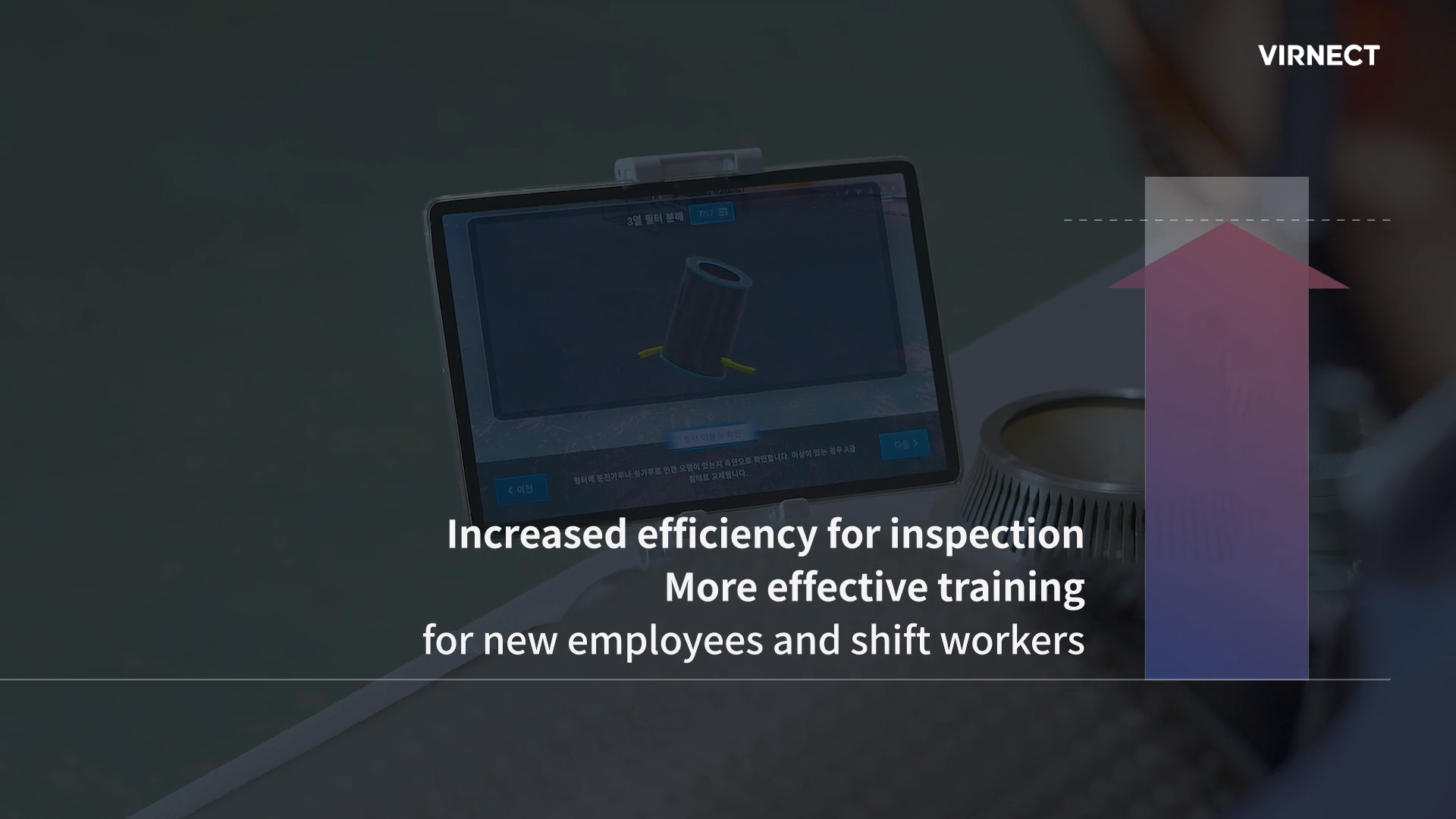
Implementing XR technology in gas inspection allowed Mirae N Seohae Energy to achieve a more reliable gas supply and a safer working environment, with reduced accidents and downtimes. On average, this means:
- A 30% reduction in training time for complex tasks.
- Over 90% reduction in costs derived from emergency response.
On the other hand, onboarding has become faster, and there has been an increase in inspection efficiency, especially for new workers.